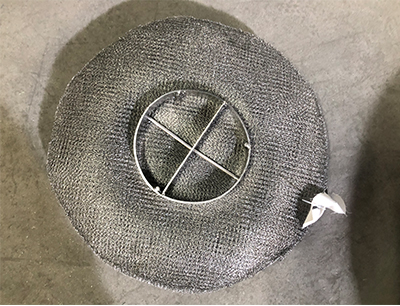
Allotype wire mesh demister
Allotype wire mesh demister
The mesh demister is mainly composed of a mesh, a mesh grid composed of a mesh block and a fixed mesh block supporting device, the mesh is a variety of materials of the gas-liquid filter, the gas-liquid filter is composed of metal wire or non-metallic wire. The non-metal wire of the gas-liquid filter is made of multiple strands of non-metal fiber twisting, which can also be a single strand of non-metal wire such as PP polypropylene and PTFE polytetrafluoroethylene engineering plastics, and can also be mixed type gas-liquid filter such as metal and polypropylene or polytetrafluoroethylene engineering plastics mixed, metal and various fiber lines mixed.
The gas-liquid filter and supporting parts used in the production of wire mesh demister are all produced by our factory in accordance with the HG/T21618-1998 wire mesh demister standard of the Ministry of Chemical Industry (the thickness and density of the demister can also be produced according to the needs of users). The mesh defoamer produced by our factory can not only filter the large liquid droplets suspended in the air stream, but also filter the small and tiny liquid droplets, which are widely used in chemical industry, petroleum, tower manufacturing, pressure vessels and other industries in the gas-liquid separation device.
Principle of wire mesh demister
The diameter of the dispersed droplets in the gas encountered in the usual chemical operation is about 0.1 to 5000μm. Generally, particles with a particle size of more than 100μm have a faster settling speed, and the separation problem is easy to solve. Droplets, usually larger than 50μm in diameter, can be separated by gravity sedimentation. The droplets above 5μm can be separated by inertial collision and centrifugation. For smaller fine fog, try to make it gather to form larger particles, or use fiber filters and electrostatic demister. The mesh demister is mainly used to separate droplets with a diameter greater than 3μm ~ 5μm, and its working principle is shown in the figure on the right. When the gas with the mist rises at a certain speed and passes through the metal mesh on the grid, the mist collides with the filaments and adheres to the surface of the filaments due to the inertia of the mist rising. The further diffusion of the fog on the surface of the filament and the gravitational settlement of the fog itself cause the fog to form larger droplets along the filament to flow to its interlace. Due to the wettability of the filaments, the surface tension of the liquid, and the capillary action of the filaments, the droplet becomes larger and larger until its own gravity exceeds the combined force of the rising buoyancy of the gas and the surface tension of the liquid, and it is separated and falls to the downstream equipment of the container. As long as the operating gas speed and other conditions are properly selected, after the gas passes through the wire mesh demister, the defrothing efficiency can reach more than 97%, and the purpose of completely removing the fog can be achieved.